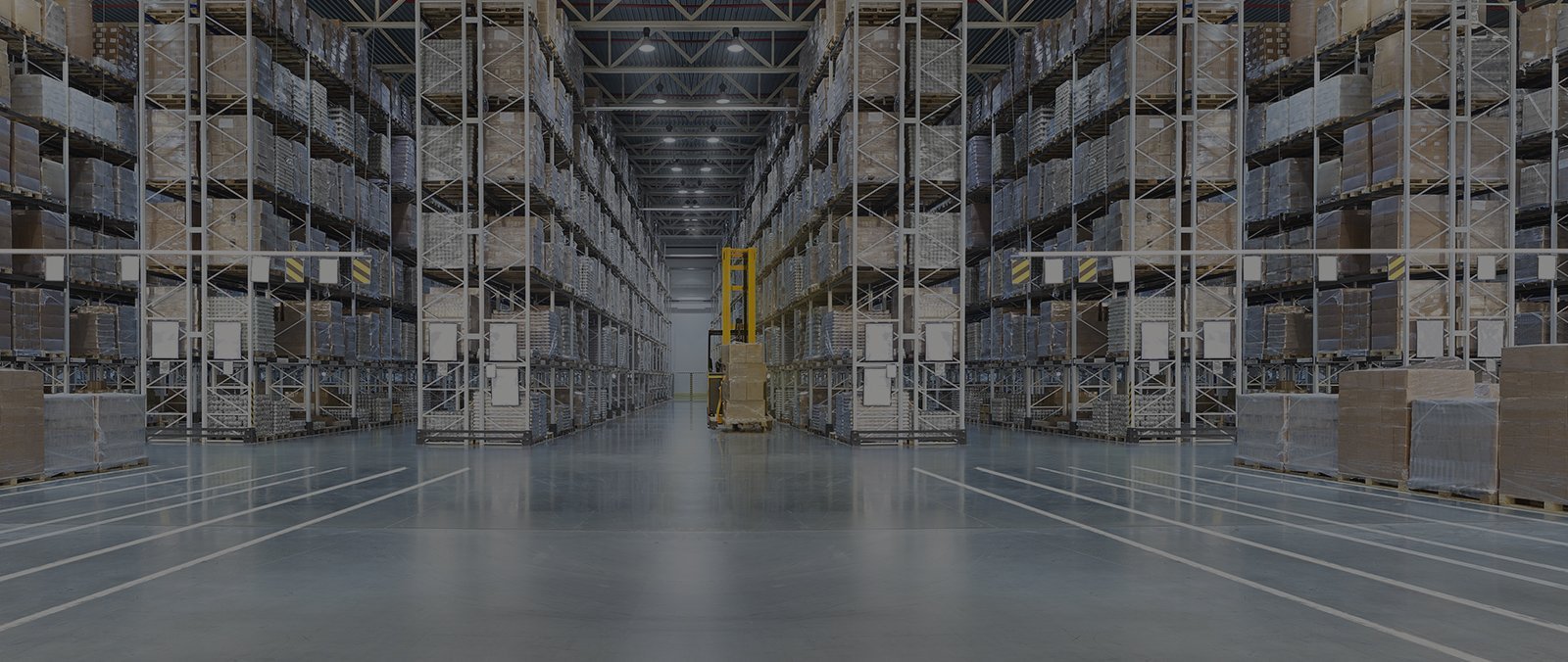
INDUSTRIAL ROBOTS
Why do you need inertial navigation system for Industrial Robots?
Inertial Navigation Systems (INS) play a role in the realm of robots, for various reasons greatly contributing to their efficiency, accuracy and overall safety in different manufacturing and automation settings. Lets explore some advantages of navigation systems for industrial robots:
- Precise Positioning and Orientation - Industrial robots often require positioning and orientation to carry out tasks with accuracy. Inertial sensors like accelerometers and gyroscopes provide real time data on the robots acceleration, velocity and orientation. This information allows for control and coordination of movements.
- Navigating Environments - Industrial environments can be dynamic with moving equipment, conveyor belts and other variables. Inertial navigation systems assist robots in navigating through these environments by providing feedback on the robots motion. This enables them to adjust their movements in time to avoid collisions or disturbances.
- High Speed Operations - Certain industrial processes demand that robots operate at speeds, such as assembly lines or packaging applications. Inertial navigation systems contribute significantly to a robots ability to maintain stability and accuracy at speeds. This ensures reliable performance.
- Navigation Redundancy - Inertial navigation can serve as a layer of redundancy alongside navigation systems, like encoders or vision systems.
Overall inertial navigation systems offer benefits that enhance the capabilities of robots across various aspects of their operations. Having sources of navigation data improves the reliability of the robots position and orientation information lowering the chances of errors or failures.
- Absence of External References - In manufacturing environments there might be situations where landmarks or markersre not available, as reference points. Inertial navigation systems function independently without relying on references making them suitable for situations where other navigation methods may not be practical.
- Real time Corrections - Inertial sensors provide feedback enabling robots to make instant adjustments to their movements. This is crucial for tasks that require precision and accuracy like pick and place operations or welding tasks.
- Automation of Complex Tasks - By offering navigation capabilities inertial navigation systems contribute to automating tasks. This autonomy proves valuable in scenarios where the robot needs to adapt to changing conditions or work in environments.
- Enhanced Path Planning and Trajectory Control - Integrating navigation data into a robots path planning and trajectory control algorithms improves its ability to accurately follow predefined paths with smoothness. This optimization brings about manufacturing processes.
- Reduced Setup Time -Inertial navigation systems help simplify and expedite the setup process, for robots. The advantage of not requiring calibration or external markers enables the robot to be deployed and reconfigured quickly for tasks.
To sum up inertial navigation systems have a role, in improving the performance of robots by supplying precise real time information, on positioning and orientation. This contributes to enhancing the efficiency, adaptability and dependability of industrial automation processes.
Contact Us for more information.