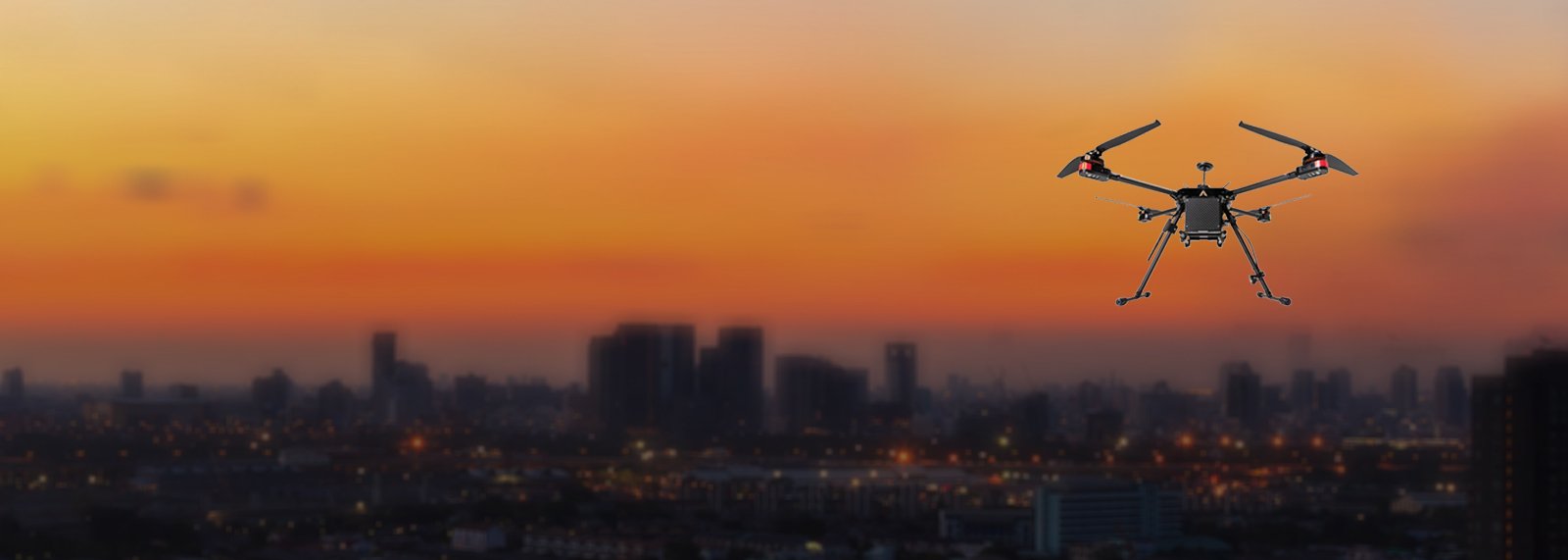
INFRASTRUCTURE INSPECTION
In today’s fast-paced world, maintaining critical infrastructure like bridges, pipelines, railways, and power lines is essential for public safety and economic stability. As infrastructure ages and the demand for inspections grows, technology is stepping in to enhance precision, efficiency, and reliability. Among the tools revolutionizing infrastructure inspection is the Inertial Navigation System (INS). But why is INS so important for this field? Let’s explore its role and benefits.
What Is an Inertial Navigation System (INS)?
An Inertial Navigation System is a self-contained navigation tool that uses accelerometers and gyroscopes to measure motion and orientation. By continuously tracking an object’s position, velocity, and attitude, INS provides precise location data even in environments where external navigation aids like GPS are unreliable.
Challenges in Infrastructure Inspection
Inspecting infrastructure involves unique challenges that demand advanced navigation solutions:
- Remote Locations - Many structures, such as pipelines or bridges, are located in remote or difficult-to-access areas with limited GPS coverage
- Dynamic Conditions - : Inspections often occur in environments with vibrations, moving machinery, or unstable surfaces
- Complex Structures - Infrastructure like tunnels, skyscrapers, and industrial plants have intricate layouts, making navigation and mapping challenging
- Safety Risks - Inspectors often work in hazardous conditions, including confined spaces, high elevations, and areas exposed to weather extremes
INS addresses these challenges with precision, reliability, and adaptability.
Why INS Is Essential for Infrastructure Inspection
1. GPS Independence
Infrastructure inspections often take place in areas where GPS signals are weak, obstructed, or unavailable, such as:
- Inside tunnels or underground pipelines
- Beneath bridges with dense structures
- Industrial facilities with metallic interference
INS provides continuous, accurate navigation in these GPS-denied environments, ensuring seamless operation and reliable data collection.
2. Real-Time Positioning
INS offers real-time tracking of an inspector's or device's position, which is critical for the following:
- Mapping the exact location of defects or wear and tear
- Ensuring comprehensive coverage of inspection areas without missing critical zones
- Guiding robotic inspection devices through complex structures or challenging terrains
3. Improved Efficiency with Sensor Fusion
When combined with other technologies, INS enhances overall inspection accuracy through sensor fusion. For example:
- LiDAR -INS ensures stable positioning for LiDAR scanners, creating precise 3D maps of structures like bridges or dams
- Cameras - INS improves image stitching and alignment for visual inspections by tracking motion and orientation.
- Ultrasound - In pipeline inspections, INS integrates with ultrasonic sensors to accurately map corrosion or blockages.
4. Resilience in Harsh Environments
Infrastructure inspection often takes place in conditions that challenge traditional navigation systems:
- Vibrations from nearby construction or machinery
- High winds or turbulent water currents when inspecting offshore structures
- Dust, smoke, or limited visibility in industrial environments
INS remains reliable in these scenarios, ensuring consistent data collection and safe operation.
5. Autonomous and Remote Inspections
With the rise of drones and robotic systems in infrastructure inspection, INS plays a vital role in enabling autonomous navigation. Applications include:
- Guiding drones along precise flight paths for power line or bridge inspections
- Steering ground-based robots through confined spaces like sewer pipes or ventilation ducts
- Ensuring stable navigation for underwater inspection systems used in dams or pipelines
Real-World Applications of INS in Infrastructure Inspection
1. Bridge Inspection
INS-equipped drones and ground robots provide detailed structural assessments, even in hard-to-reach areas beneath the bridge deck or inside support structures.
2. Pipeline Monitoring
INS enables autonomous inspection robots to navigate through long, buried pipelines, accurately identifying corrosion, leaks, or blockages without relying on GPS.
3. Power Line Surveys
INS ensures stable flight paths for drones inspecting power lines, even in remote or windy locations, while capturing high-resolution images and thermal data.
4. Railway Maintenance
INS supports the precise navigation of inspection vehicles along railway tracks, ensuring detailed assessments of rail conditions and detecting potential hazards.
5. Offshore Structures
INS is crucial for underwater inspections of offshore oil rigs, wind turbines, and undersea pipelines, providing reliable navigation in GPS-denied environments.
The Benefits of Using INS for Infrastructure Inspection
- Increased Accuracy - INS delivers precise positional data, ensuring thorough inspections without missing critical areas
- Time and Cost Savings - By enabling autonomous or semi-autonomous systems, INS reduces the time and manpower required for inspections
- Enhanced Safety - With INS, inspectors can operate drones and robots in hazardous environments, minimizing human exposure to risks
- Comprehensive Data Collection - INS ensures reliable navigation for mapping and imaging systems, providing detailed and actionable insights.
Conclusion
Inertial Navigation Systems are transforming the way we inspect and maintain critical infrastructure. Their ability to navigate without external signals, provide real-time data, and integrate seamlessly with other sensors makes them indispensable for efficient, accurate, and safe inspections. Whether inspecting pipelines, bridges, or offshore structures, INS ensures that no corner is left unexplored and no defect goes undetected.
Contact Us for more information.